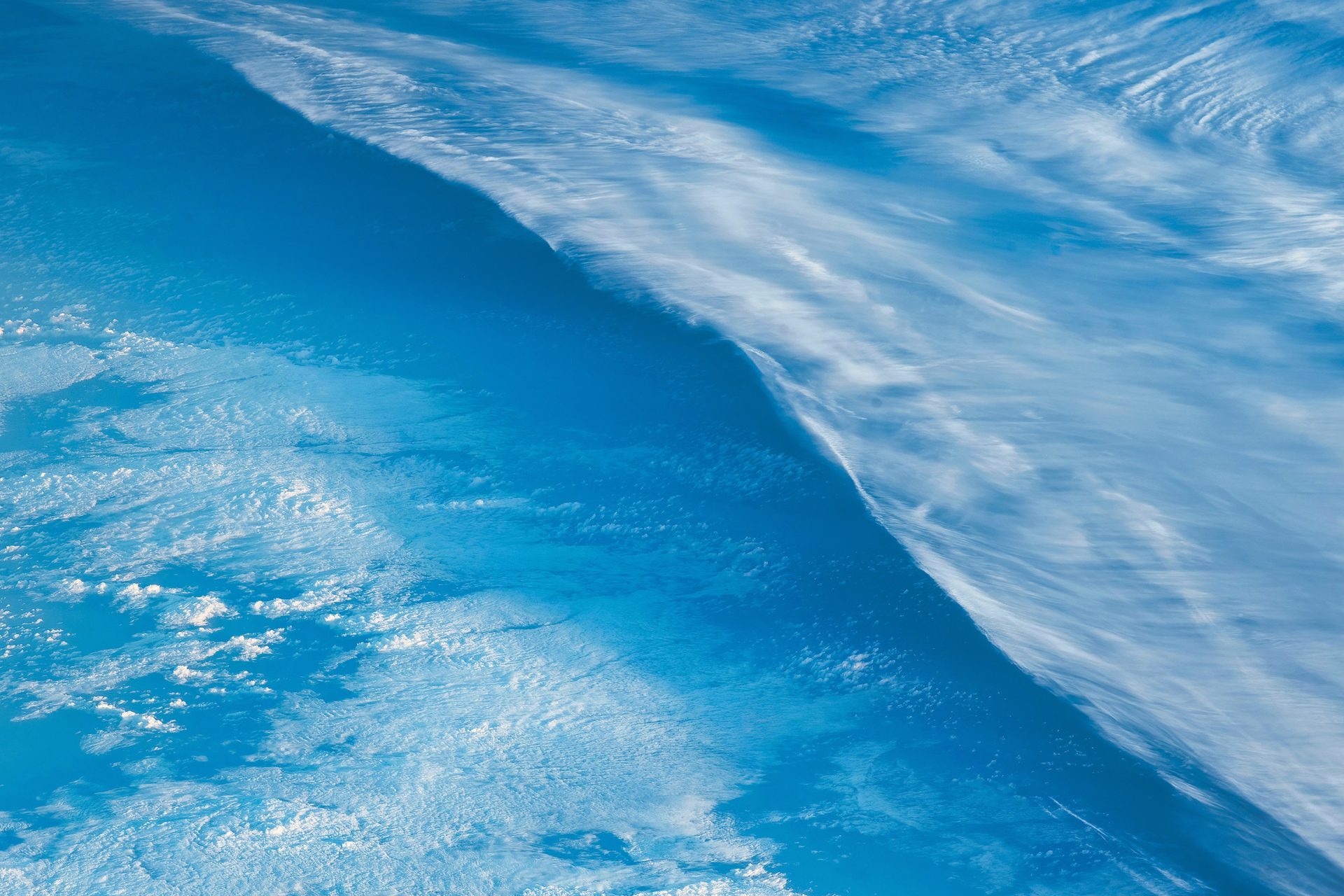
Welcome to the beginning of a clean new industrial era.
Powered by Coolbrook RotoDynamic Technology.
The new standard in industrial electrification
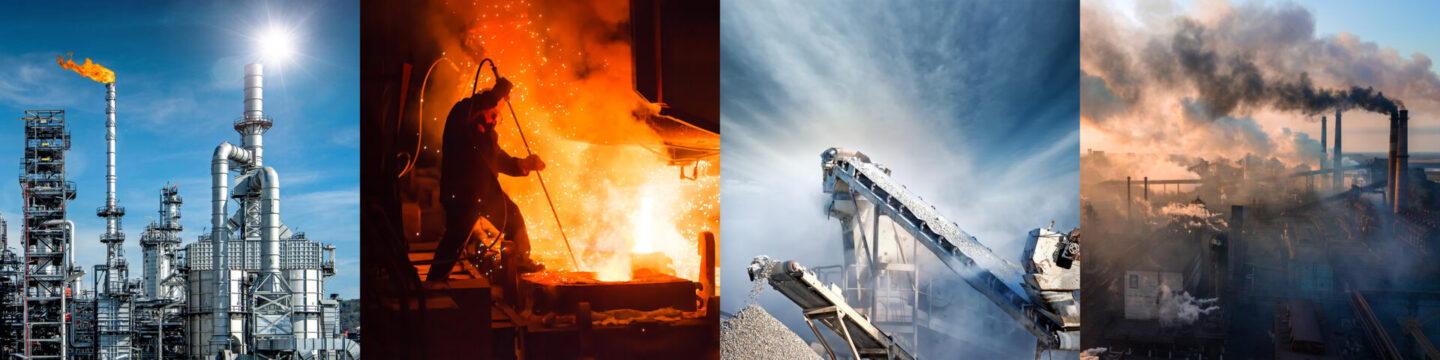
Coolbrook’s patented RotoDynamic Technology has the potential to reduce global annual CO2 emissions in hard-to-abate heavy industry sectors by 30% (2.4 Gt) through electrification and decarbonization powered by clean, renewable energy.
The technology has the potential to reach temperatures of 1700 °C, and it can replace fossil-fired steam crackers to reach 100% CO2 free olefin production in petrochemical industry.
It can also electrify high temperature process heating in the production of cement, steel and iron, and chemicals, and more.
Everything that can be electrified must be
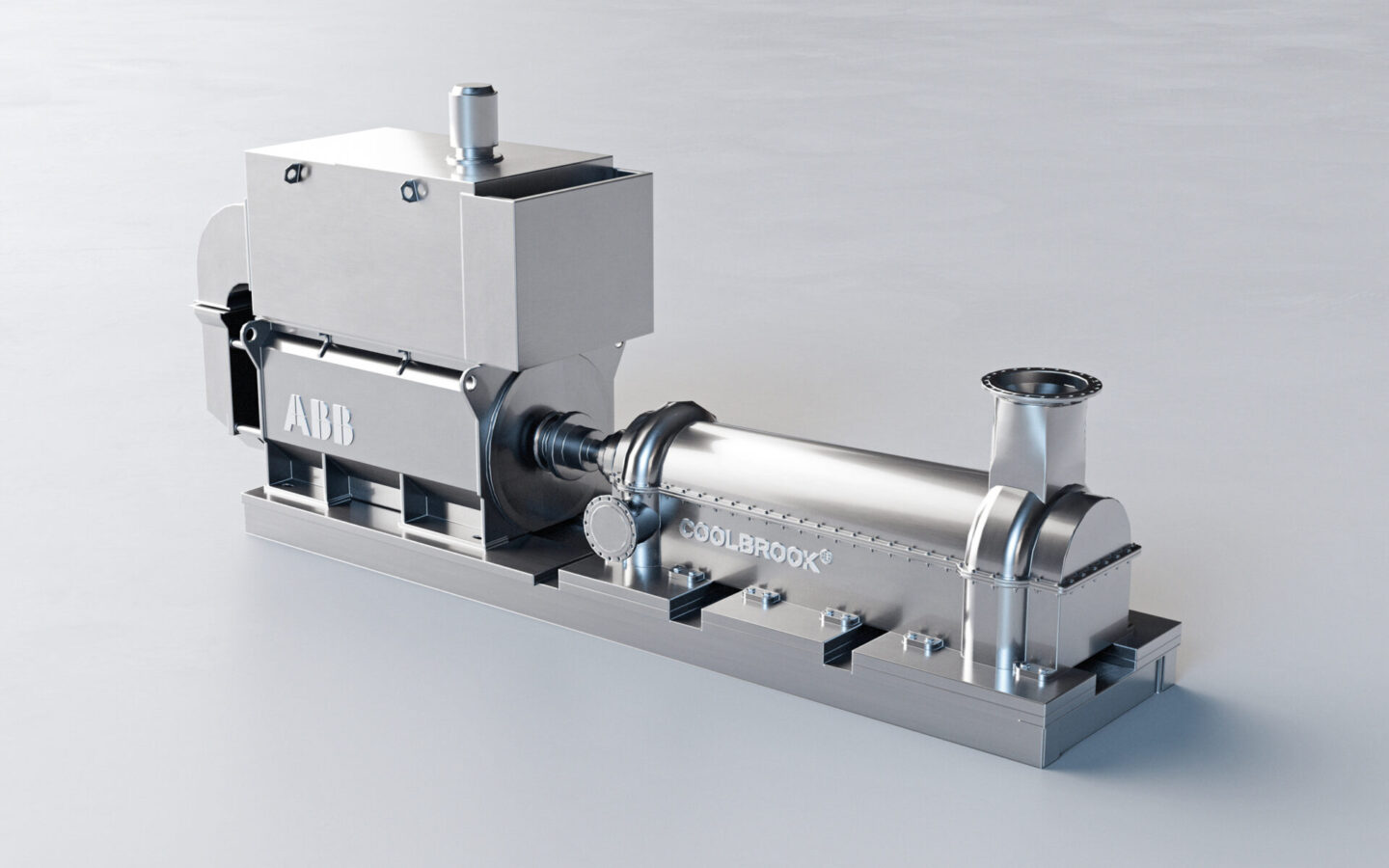
Coolbrook’s groundbreaking RotoDynamic Technology can electrify industrial sectors that until now have been considered almost impossible to electrify. We can electrify and decarbonize processes up to 1700 °C, where no other electric technology is able to go. Hard-to-abate is now possible-to-abate.
Electrification of heavy industrial processes across hard-to-abate industry sectors is the key to achieving the required emission reductions and to speed up the transition to carbon-zero.
Direct electrification with clean electricity is the superior alternative towards zero carbon industrial production in all applicable cases due to higher energy efficiency and lower cost.
01
ENERGY SOURCE
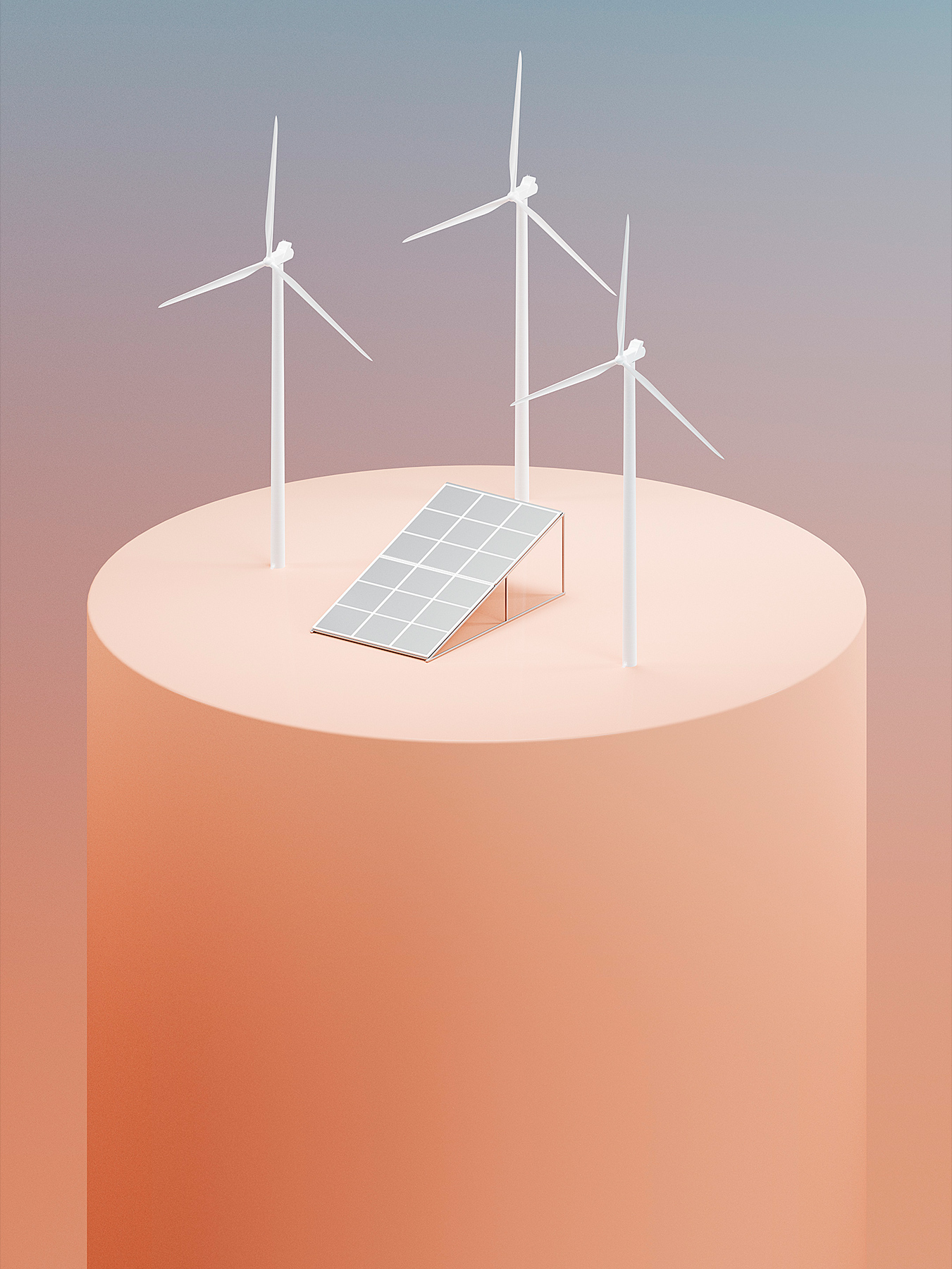
Renewable energy is generated by wind, solar and hydro power.
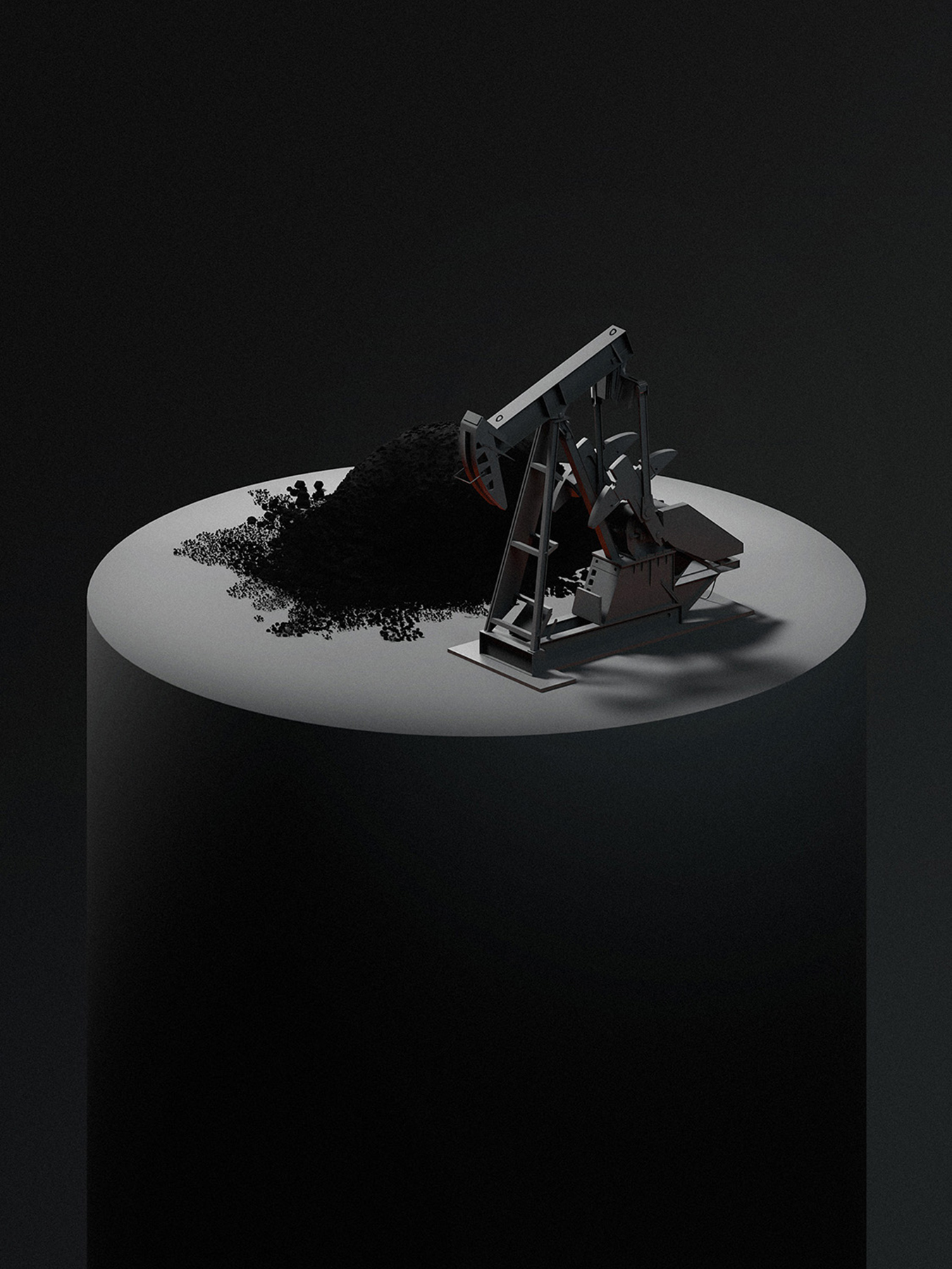
Fossil fuels such as oil, gas and coal are extracted from the earth.
02
Emissions in industrial production
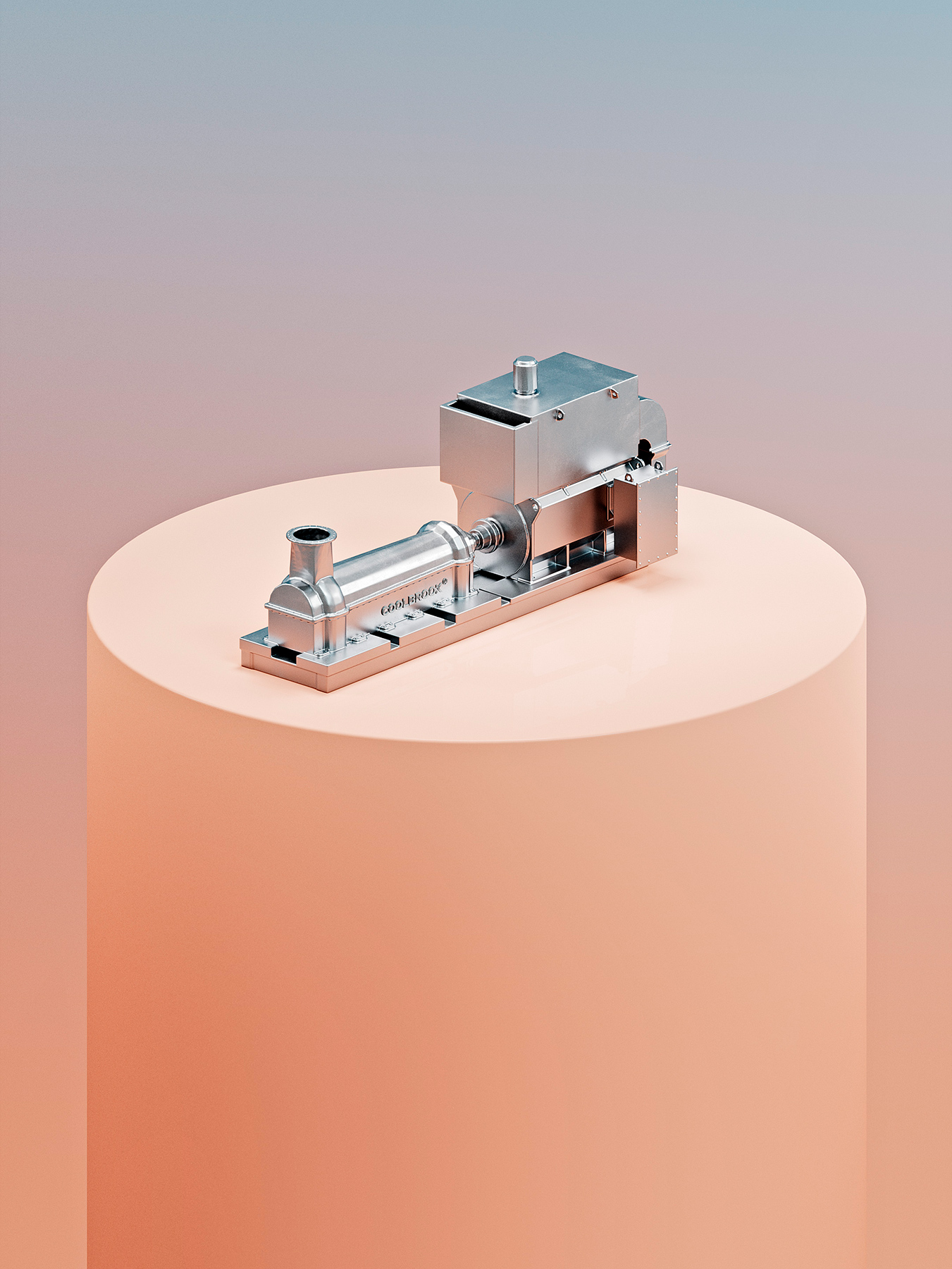
Renewable energy powers the RotoDynamic Technology with the potential to reduce up to 2.4 billion tons of CO2 emissions in industrial processes.
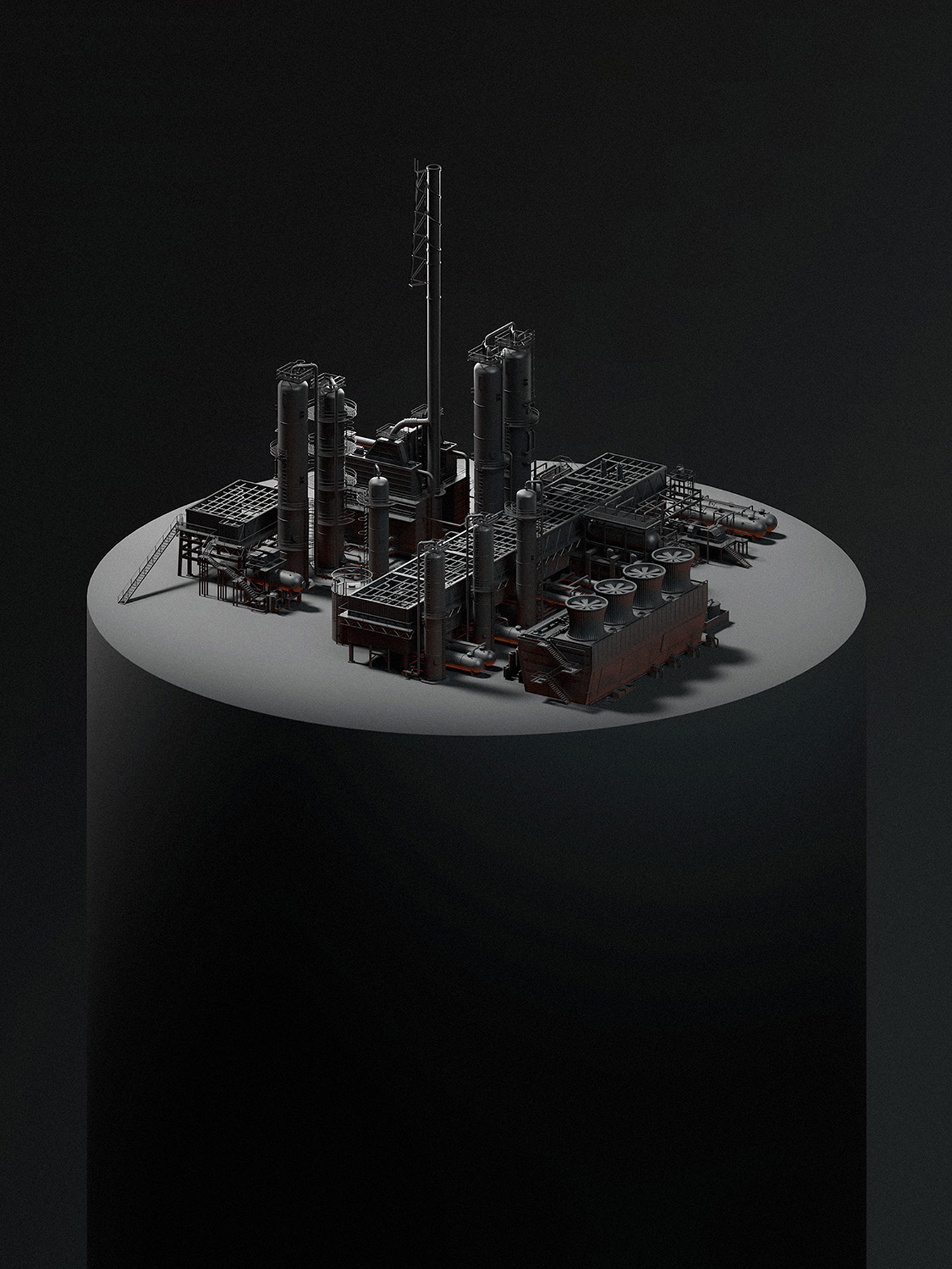
Fossil fuels are burned in heavy industries such as cement, steel, petrochemicals and chemicals to reach the required high process temperatures. This generates 8.7 billion tons of CO2 emissions annually.
03
End-product carbon footprint
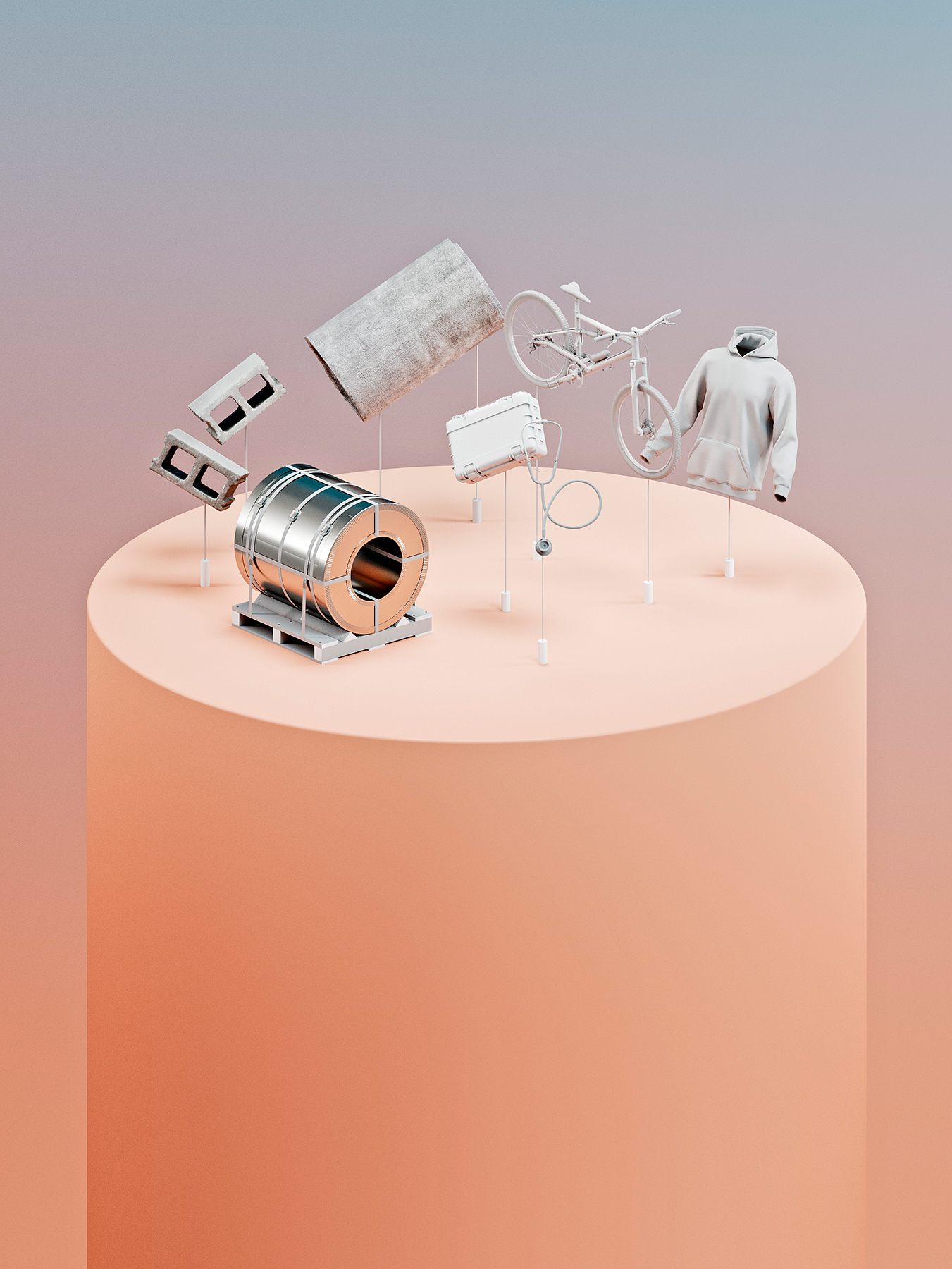
The products and materials produced with coolbrook technology carry a substantially lighter CO2 footprint.
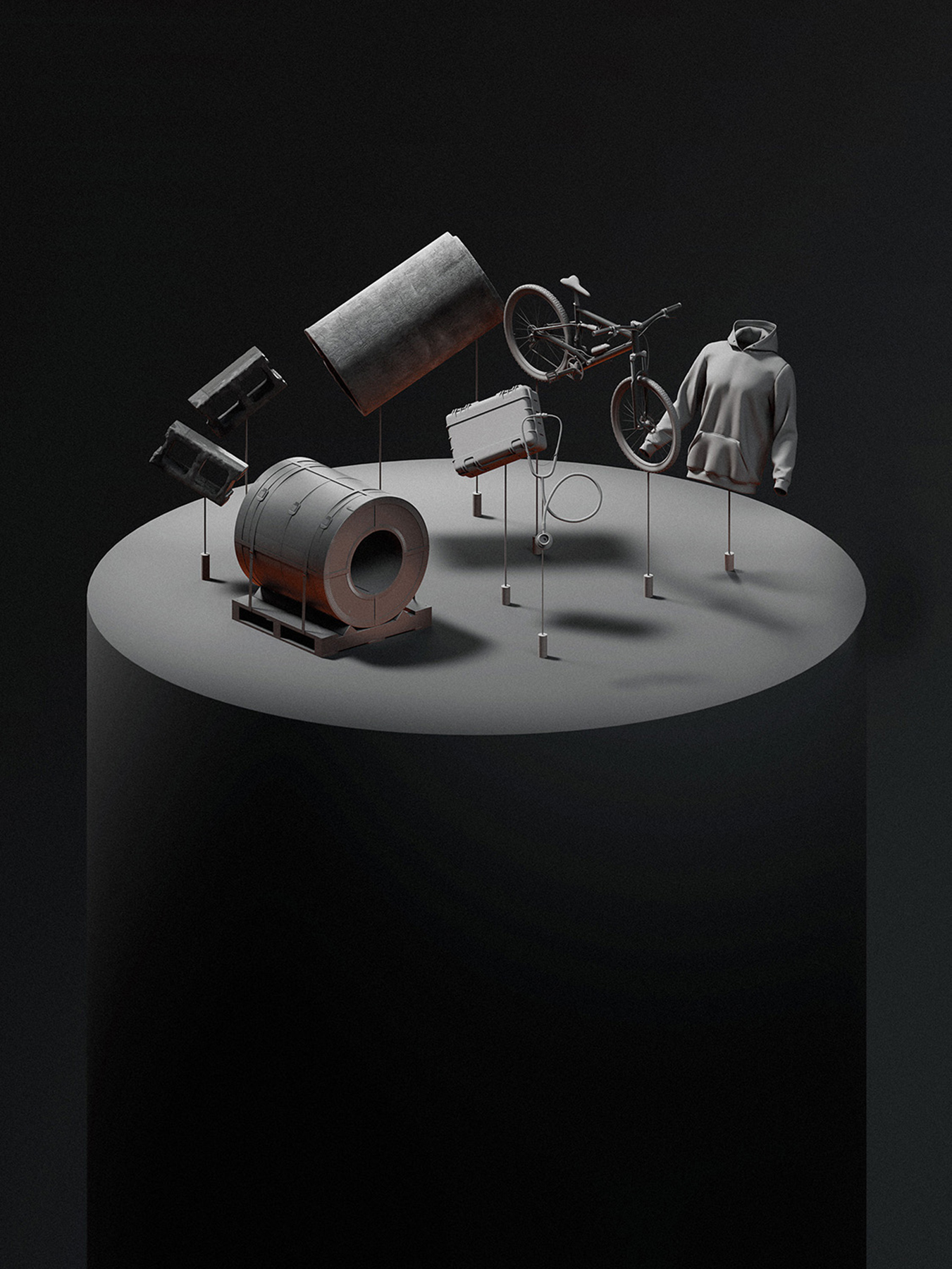
the products and raw materials essential to our everyday lives carry a heavy CO2 footprint.
For industries
Electrifying the hard-to-abate industries – the world’s most polluting industrial processes
Coolbrook’s RotoDynamic HeaterTM (RDH) and RotoDynamic ReactorTM (RDR) can be used to electrify and decarbonize traditionally hard-to-abate industrial processes, including the production of steel and iron, cement, pulp and paper, petrochemicals and chemicals.
We have teamed up with the world’s leading technology partners and industrial customers for commercial roll-out of the RotoDynamic Technology at scale in the mid-2020’s.
A comprehensive and growing partner ecosystem
We are already partnering with some of the world’s leading industrial producers, technology companies and academic partners in development of our technology and to ensure fast and broad adoption of our electrification technology for industrial electrification.
Our partners and customers include ABB, Linde Engineering, Schmidtsche Schack, Tenova, Shell, Braskem, SABIC, CEMEX, UltraTech Cement, Ambuja Cements (part of Adani Group), JSW Group, ArcelorMittal, as well as Ghent University, University of Oxford, University of Cambridge. We also partner with Netherlands Enterprise Agency, Business Finland, Climate Leadership Coalition CLC and Brightlands.
We share the sense of urgency with our partners and customers for cutting CO2 emissions across various industries and believe that together we can create the positive change the world needs.
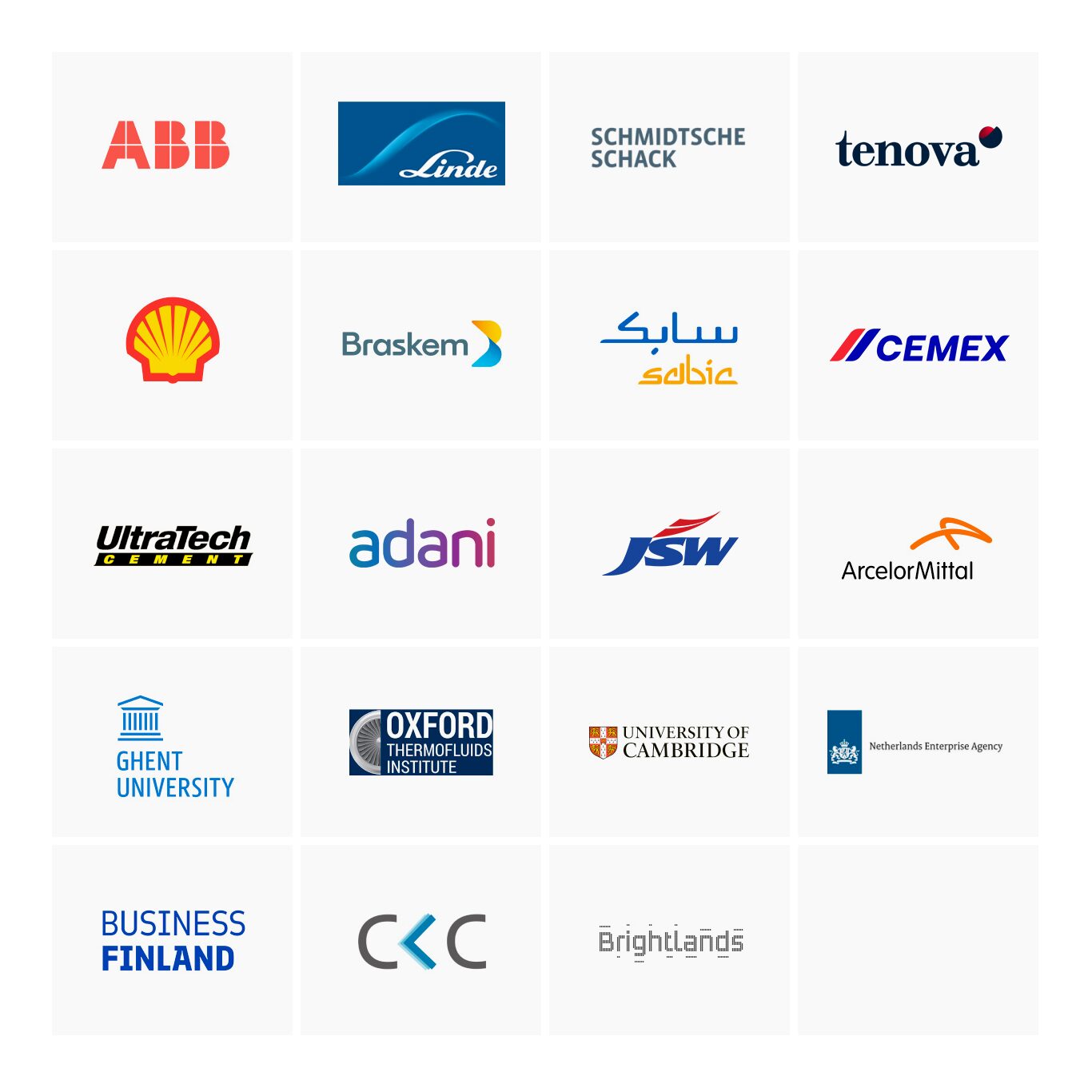
Timeline
Technology proven and first product commercially available
We’re partnering with some of the brightest minds and biggest industrial players in the world to make our RotoDynamic Technology the new global standard in the electrification of traditionally highly polluting industrial production processes. We have proven the technology and its capabilities at our pilot plant in Geleen, the Netherlands, since December 2022, and our first product has been ready to order since early 2024.
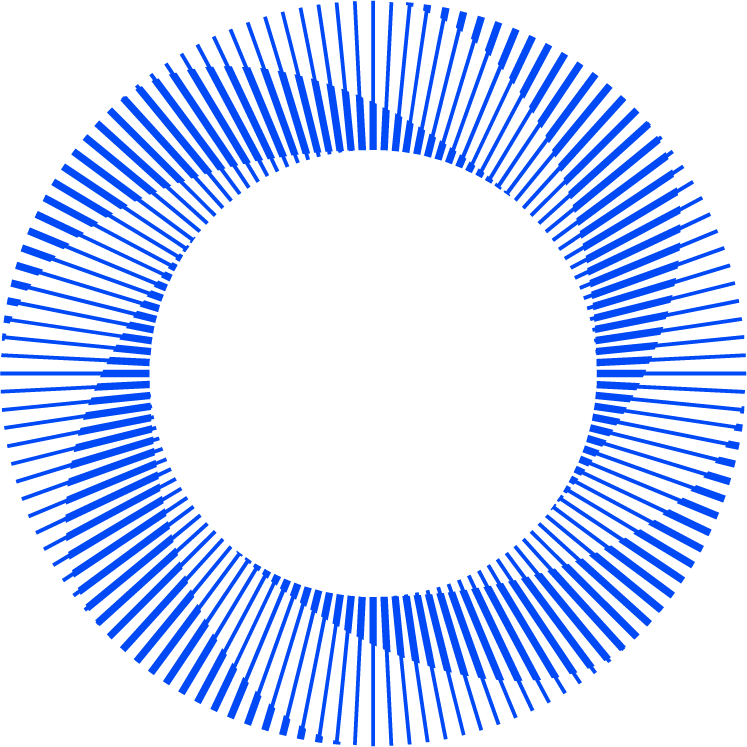
2011 – 2020
- Small scale pilot and proof of concept for technology
- Fundamental technology development with world leading universities
- Establishment of strong patent portfolio
2021 – 2023
- Construction and operations of large scale pilot in Geleen, the Netherlands
- Temperatures of 1,000+°C reached (RDH)
- Naphtha successfully cracked (RDR)
- Partner engagement across key industrial and academic sectors
2024 →
- First commercial RDH product launched in the beginning of 2024
- First units delivered in 2025
- Next products (RDR and Next Generation RDH) launched in 2025-2026
- Further expansion of partner network
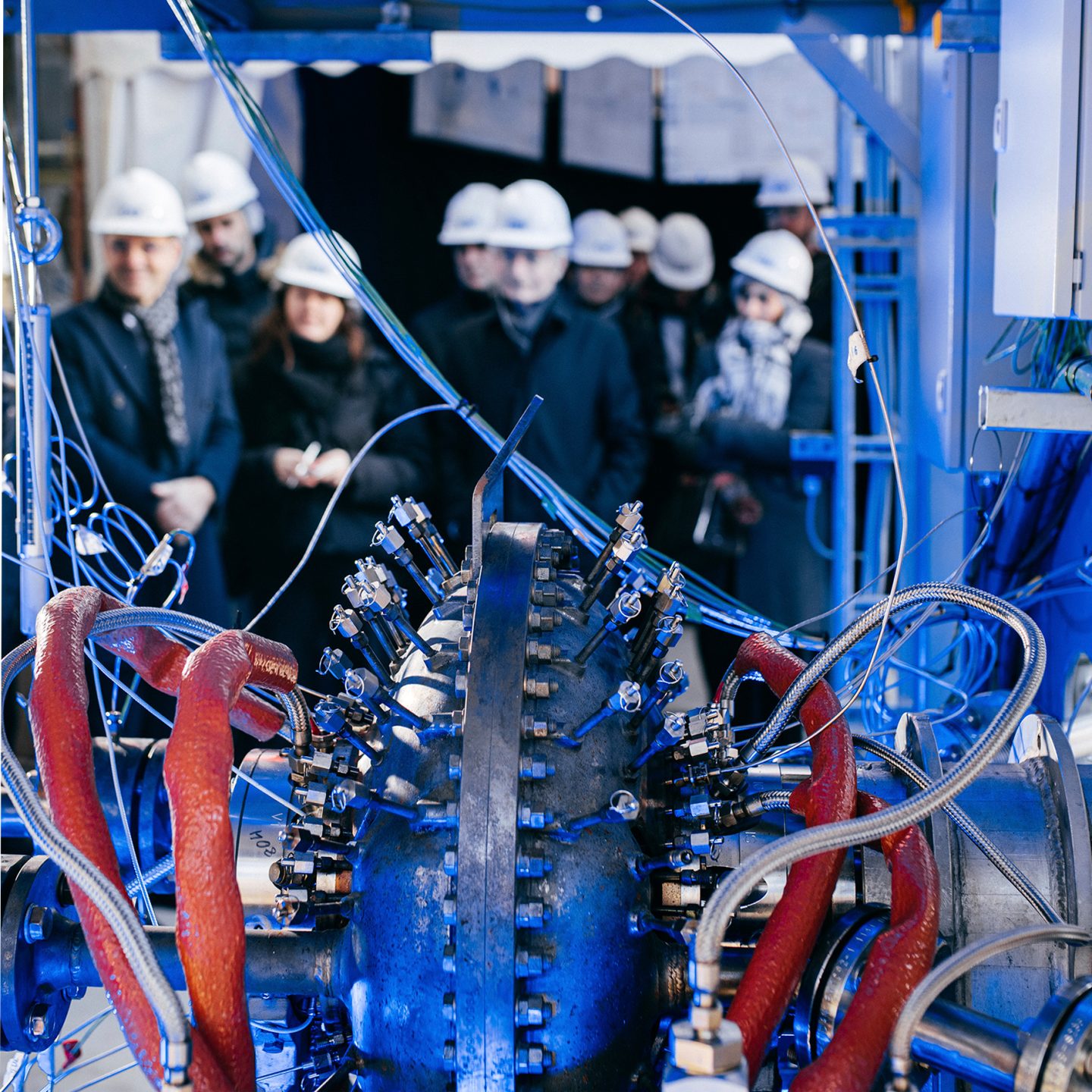
RotoDynamic Technology has been proven at large scale
RotoDynamic Technology has been proven through pilot testing at a large-scale test unit at the Brightlands Chemelot Campus in Geleen, the Netherlands.
The main targets of the pilot project:
- Demonstrate the use of RotoDynamic Heater™ (RDH) technology for high-temperature process heating with inert gases, such as: air, nitrogen, methane, steam, CO2
- Demonstrate the RotoDynamic Reactor™ (RDR) technology and its reliability for hydrocarbon cracking to stakeholders in the petrochemical industry
- Validate modelling (fluid dynamics) and design parameters and to establish basis for first customer projects